Labor shortages, rising costs for raw materials be it lumber or chemicals, and the importance of private-public partnerships in manufacturing critical supply chains were the main topics of discussion during a House committee hearing on Wednesday. But missing from the debate was a discussion on reshoring American manufacturing as another solution. More goods made here means fewer goods waiting to get into ports.
Rep. Carolyn Bourdeaux (D-GA-7) was the best example of the day. She said supply chain problems have been getting worse over the last two months.
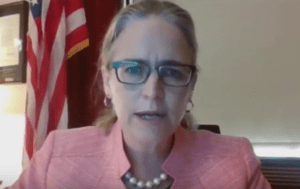
Rep. Carolyn Bordeaux of Georgia said a company in her district had to shut down production due to supply constraints stemming from China.
“In my district, Metcam Metal Fabricators had to shut down production of certain items due to a shortage of titanium dioxide that is an important component almost exclusively available from China,” she told the House Committee on Small Business’s Subcommittee on Oversight, Investigations and Regulations on October 20. The hearing was titled “Global Supply Chains and Small Business Trade Challenges.”
Bourdeaux said Metcam’s business led to restrictions of manufacturing at Carrier, a multinational famous for heating and cooling systems, due to Metcam. She laid part of the blame on just-in-time manufacturing models and globalized supply chains.
“We have not matched that change with sufficient government review and support for supply chains of critical goods,” she said, adding the line of the day: “This is not only an economics issue. This is a national security issue.”
The CPA Reshoring Index
CPA’s proprietary index measuring the return of manufacturing businesses from abroad shows that dependence on imports has been rising steadily over the last 18 years. Imports accounted for 30% of all manufactured goods consumed in the U.S. last year, up 8 percentage points in a decade despite tariffs.
Keep in mind that tariffs, we were told by the anti-tariff crowd, were supposed to crush demand and raise prices. Instead, exporting companies found ways around those tariffs by relocating manufacturing to non-tariffed countries (like China in Southeast Asia), absorbed the entirety of tariff costs themselves or shared it with their buyers.
Some sectors are almost fully import-dependent. Clothing imports account for around 90% of the local market share.
“Our dependence on imports, combined with growing reliance on one or a tiny number of suppliers, many of them in China, lies at the root of the global supply-chain snafu the world is experiencing right now,” said Jeff Ferry, chief economist for CPA. “The best solution would be to begin unwinding these excessively long and complex global supply chains and bringing production back closer to home.”
House Committee talks ‘Solutions’
Congress is not short of ideas on issues related to the supply chain. Be it reshoring critical medication, or the infrastructure bill that will set aside billions for ports or roads.
Earlier this month, Bourdeaux introduced the Supply Chain Health and Integrity Act, which would create an office of supply chain resiliency inside the Department of Commerce that is responsible for producing a national strategic plan for manufacturing and industrial innovation that will “guide our nations efforts to secure our most critical supply chains,” she said.
Some of this work is already ongoing. Last year, the Food and Drug Administration developed a list of hundreds of medications it deemed essential. Mostly all of it was imported.
Months before the FDA list was finally published, the government’s Biological Advanced Research and Development Authority, aka BARDA gave local generic drug maker Phlow $354 million in funding to produce essential medicine. Phlow is also building the United States’ first Strategic Active Pharmaceutical Ingredients Reserve, a long-term, national stockpile to secure key ingredients used to manufacture the most essential medicines, reducing import demand.
“Public and private partnership will be key to this solution,” said hearing witness Chris O’Brien, chief commercial officer for logistics firm R.H. Robinson. He was not speaking to pharmaceuticals directly but did mention his company’s financing from his home state of Minnesota during the crisis for personal protection equipment manufacturing and delivery at the height of the pandemic in 2020.
O’Brien also said he doubted manufacturers would move away from lean manufacturing because this keeps costs lower and enables companies to compete with cheaper producers in Mexico and Asia, where the currency differential alone is astronomical.
Majority of Businesses Not Thinking About Reshoring
Rep. Beth Van Duyne (R-TX-24), the ranking member on the Committee, started the day by quoting from a Small Business Association (the NFIB) survey that showed 90% of survey respondents had said that the current supply chain mess is impacting their business. At least 50% said they were experiencing product delays, and 25% said they were experiencing slower delivery times to customers with another 20% saying they will “rethink” their current supply chain.
That this number is so low – at just 20% — suggests most businesses are still not looking to reshore even after nearly three years of higher tariffs on more than $300 billion worth of goods from China. This should serve as a reminder that China is not our only deficit market. The European Union is closing in on them. As is Mexico.
Many CPA members who source the majority of their goods domestically are not having problems with their supply chains, but are having serious problems finding workers.
“Worker shortages have hindered the ability to get products out,” Van Duyne said, citing a WSJ article during the hearing that reported 51% of small businesses had unfilled job openings, a 48-year record high for the third consecutive month. “Container ships have no available slips to unload and small businesses cannot find workers. Without the products or workers, store shelves around the country are becoming increasingly empty,” Van Duyne said.
“Congress needs to focus upon building a minimum domestic production capacity for goods when shortages appear or when there is a risk of shortage. This will ensure price and supply stability, protect against geostrategic vulnerabilities, and create good paying jobs. All trade and industrial strategy tools should be on the table to rebuild these demonstrated shortages sectors that harm our national economic interests.” – Michael Stumo, CEO of the Coalition for a Prosperous America
If the U.S. was not so import-heavy, this would not be as big a problem as it today. While global supply chains are not going away anytime soon, and numerous factories will always need parts from abroad – whether its printed circuit boards from Mexico, Swedish steel, or German engines – it is clear that companies with stronger domestic supply chains are better off than those dependent on foreign supply chains.
The Chairman Blames ‘Trade War’ Tariffs
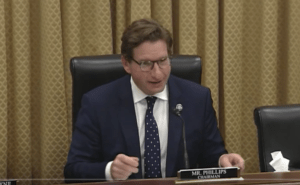
Committee Chairman Dean Phillips from Minnesota blamed trade war tariffs for part of the supply chain bottlenecks. CPA respectfully disagrees that tariffs caused any of these problems.
Chairman Dean Phillips (D-MN-3) said “port closures in Shanghai can lead to short supply of tools in a tool shop in the U.S.” He added that such news doesn’t make it on the cable news shows, but it actually does. The supply chain crisis is one of the biggest problems facing the country at the moment.
Phillips blamed lockdowns and “trade wars” for the problem.
O’Brien chimed in, seemingly in agreement.
“The trade war has caused higher prices to small businesses,” O’Brien said. “They are wondering if tariffs are likely to continue or expire. Congress and the administration can provide more signals to small businesses regarding the direction of the trade war so they can make long-term decisions.”
CPA believes American businesses have been warned of tariff risks since 2017. Companies have had four years to remap their supply chains away from China, but many have chosen not to, assuming the status-quo would return.
Protectionism has been intruding on supply chains at least since 2008 when the Doha round of global trade talks collapsed. The U.S.-China trade war took those frictions to a new level. In its wake, the U.S., China and Europe are all pursuing self-sufficiency in key sectors such as semiconductors and batteries. Other threats loom, such as green tariffs on high-carbon imports. Meanwhile, arbitrary import bans and detentions are now routine parts of China’s foreign-policy tool kit, as export controls are part of the U.S.’s. – Greg Ip, “Supply-Chain Crisis Fuels Latest Retreat From Globalization”, Wall Street Journal, October 20, 2021.
Moreover, O’Brien’s comment in response to Chairman Phillips is a good example of how inflation will be blamed on tariffs, leading to an increasing call to remove protections on key industries that will either be forced to stop investing or will manufacture more abroad. The other possibility is that more, costly government subsidies will be required to keep some of these companies in business.
Congress should prepare for this argument. While inflation weakening the tariff argument serves the interests of some small businesses, it primarily suits the anti-tariff position at the global corporations who those small businesses serve. Global companies would likely replace domestic suppliers for cheaper ones elsewhere soon after China tariffs are removed.
Chairman Phillips knows that small (and mid-sized) businesses will have a difficult time weathering that storm. He said that they are currently having a hard time dealing with the big multinational shipping giants like Maersk. Imagine trying to convince their big multinational customers like Cummins to buy a widget from them now that they have become 20% cheaper due to tariff removals on the same items made in China.
“Big firms can negotiate with shipping companies to lower prices, but small companies cannot,” Phillips said, adding we have to make the supply chain more resilient. “The Federal government has to work with the private sector to find solutions…because we already know the problems,” he said.
Phlow and BARDA are good examples of finding a solution.
If the infrastructure bill ever passes and we get expansion of ports, that might help. But if the investment in ports is just a bigger door opening for more imports, then it is the exact opposite of supply chain resilience. Yes, China ports are gigantic. But that is because China has made investments in being the global manufacturing hub. Those ports were made with exports in mind. Without support for domestic supply chains, expanding U.S. ports will be built with imports in mind.
Christine Lantinen, president and owner of Minnesota candy maker Maud Borup Inc doesn’t really need to rely on imports, but she can’t get employees. Her company is over 100 years old. “At 200 employees, I am down maybe 100 for an optimal number. Since December we have instituted a 36% hourly salary increase and we still have trouble recruiting workers.” Recruiting workers was her biggest problem.
Record subsidies to individuals during the pandemic is one reason people have not yet returned to the labor market, many manufacturing companies are saying.
“The situation is so severe, that despite the purchase of six acres of land, we put our expansion plans on hold. This is unsustainable,” Lantinen said.
Global supply chains today are too lengthy, too complex, too interdependent, too polluting and too subject to the risk of cascading delivery failure to be sustainable.
Companies that are doing well, like Toyota and Tesla, are those that have always made it a priority to keep suppliers close to the point of final production.
House Committee Hearing on Small Business Supply Chains Forgets About Reshoring
Labor shortages, rising costs for raw materials be it lumber or chemicals, and the importance of private-public partnerships in manufacturing critical supply chains were the main topics of discussion during a House committee hearing on Wednesday. But missing from the debate was a discussion on reshoring American manufacturing as another solution. More goods made here means fewer goods waiting to get into ports.
Rep. Carolyn Bourdeaux (D-GA-7) was the best example of the day. She said supply chain problems have been getting worse over the last two months.
Rep. Carolyn Bordeaux of Georgia said a company in her district had to shut down production due to supply constraints stemming from China.
“In my district, Metcam Metal Fabricators had to shut down production of certain items due to a shortage of titanium dioxide that is an important component almost exclusively available from China,” she told the House Committee on Small Business’s Subcommittee on Oversight, Investigations and Regulations on October 20. The hearing was titled “Global Supply Chains and Small Business Trade Challenges.”
Bourdeaux said Metcam’s business led to restrictions of manufacturing at Carrier, a multinational famous for heating and cooling systems, due to Metcam. She laid part of the blame on just-in-time manufacturing models and globalized supply chains.
“We have not matched that change with sufficient government review and support for supply chains of critical goods,” she said, adding the line of the day: “This is not only an economics issue. This is a national security issue.”
The CPA Reshoring Index
CPA’s proprietary index measuring the return of manufacturing businesses from abroad shows that dependence on imports has been rising steadily over the last 18 years. Imports accounted for 30% of all manufactured goods consumed in the U.S. last year, up 8 percentage points in a decade despite tariffs.
Keep in mind that tariffs, we were told by the anti-tariff crowd, were supposed to crush demand and raise prices. Instead, exporting companies found ways around those tariffs by relocating manufacturing to non-tariffed countries (like China in Southeast Asia), absorbed the entirety of tariff costs themselves or shared it with their buyers.
Some sectors are almost fully import-dependent. Clothing imports account for around 90% of the local market share.
“Our dependence on imports, combined with growing reliance on one or a tiny number of suppliers, many of them in China, lies at the root of the global supply-chain snafu the world is experiencing right now,” said Jeff Ferry, chief economist for CPA. “The best solution would be to begin unwinding these excessively long and complex global supply chains and bringing production back closer to home.”
House Committee talks ‘Solutions’
Congress is not short of ideas on issues related to the supply chain. Be it reshoring critical medication, or the infrastructure bill that will set aside billions for ports or roads.
Earlier this month, Bourdeaux introduced the Supply Chain Health and Integrity Act, which would create an office of supply chain resiliency inside the Department of Commerce that is responsible for producing a national strategic plan for manufacturing and industrial innovation that will “guide our nations efforts to secure our most critical supply chains,” she said.
Some of this work is already ongoing. Last year, the Food and Drug Administration developed a list of hundreds of medications it deemed essential. Mostly all of it was imported.
Months before the FDA list was finally published, the government’s Biological Advanced Research and Development Authority, aka BARDA gave local generic drug maker Phlow $354 million in funding to produce essential medicine. Phlow is also building the United States’ first Strategic Active Pharmaceutical Ingredients Reserve, a long-term, national stockpile to secure key ingredients used to manufacture the most essential medicines, reducing import demand.
“Public and private partnership will be key to this solution,” said hearing witness Chris O’Brien, chief commercial officer for logistics firm R.H. Robinson. He was not speaking to pharmaceuticals directly but did mention his company’s financing from his home state of Minnesota during the crisis for personal protection equipment manufacturing and delivery at the height of the pandemic in 2020.
O’Brien also said he doubted manufacturers would move away from lean manufacturing because this keeps costs lower and enables companies to compete with cheaper producers in Mexico and Asia, where the currency differential alone is astronomical.
Majority of Businesses Not Thinking About Reshoring
Rep. Beth Van Duyne (R-TX-24), the ranking member on the Committee, started the day by quoting from a Small Business Association (the NFIB) survey that showed 90% of survey respondents had said that the current supply chain mess is impacting their business. At least 50% said they were experiencing product delays, and 25% said they were experiencing slower delivery times to customers with another 20% saying they will “rethink” their current supply chain.
That this number is so low – at just 20% — suggests most businesses are still not looking to reshore even after nearly three years of higher tariffs on more than $300 billion worth of goods from China. This should serve as a reminder that China is not our only deficit market. The European Union is closing in on them. As is Mexico.
Many CPA members who source the majority of their goods domestically are not having problems with their supply chains, but are having serious problems finding workers.
“Worker shortages have hindered the ability to get products out,” Van Duyne said, citing a WSJ article during the hearing that reported 51% of small businesses had unfilled job openings, a 48-year record high for the third consecutive month. “Container ships have no available slips to unload and small businesses cannot find workers. Without the products or workers, store shelves around the country are becoming increasingly empty,” Van Duyne said.
If the U.S. was not so import-heavy, this would not be as big a problem as it today. While global supply chains are not going away anytime soon, and numerous factories will always need parts from abroad – whether its printed circuit boards from Mexico, Swedish steel, or German engines – it is clear that companies with stronger domestic supply chains are better off than those dependent on foreign supply chains.
The Chairman Blames ‘Trade War’ Tariffs
Committee Chairman Dean Phillips from Minnesota blamed trade war tariffs for part of the supply chain bottlenecks. CPA respectfully disagrees that tariffs caused any of these problems.
Chairman Dean Phillips (D-MN-3) said “port closures in Shanghai can lead to short supply of tools in a tool shop in the U.S.” He added that such news doesn’t make it on the cable news shows, but it actually does. The supply chain crisis is one of the biggest problems facing the country at the moment.
Phillips blamed lockdowns and “trade wars” for the problem.
O’Brien chimed in, seemingly in agreement.
“The trade war has caused higher prices to small businesses,” O’Brien said. “They are wondering if tariffs are likely to continue or expire. Congress and the administration can provide more signals to small businesses regarding the direction of the trade war so they can make long-term decisions.”
CPA believes American businesses have been warned of tariff risks since 2017. Companies have had four years to remap their supply chains away from China, but many have chosen not to, assuming the status-quo would return.
Moreover, O’Brien’s comment in response to Chairman Phillips is a good example of how inflation will be blamed on tariffs, leading to an increasing call to remove protections on key industries that will either be forced to stop investing or will manufacture more abroad. The other possibility is that more, costly government subsidies will be required to keep some of these companies in business.
Congress should prepare for this argument. While inflation weakening the tariff argument serves the interests of some small businesses, it primarily suits the anti-tariff position at the global corporations who those small businesses serve. Global companies would likely replace domestic suppliers for cheaper ones elsewhere soon after China tariffs are removed.
“Big firms can negotiate with shipping companies to lower prices, but small companies cannot,” Phillips said, adding we have to make the supply chain more resilient. “The Federal government has to work with the private sector to find solutions…because we already know the problems,” he said.
Phlow and BARDA are good examples of finding a solution.
Christine Lantinen, president and owner of Minnesota candy maker Maud Borup Inc doesn’t really need to rely on imports, but she can’t get employees. Her company is over 100 years old. “At 200 employees, I am down maybe 100 for an optimal number. Since December we have instituted a 36% hourly salary increase and we still have trouble recruiting workers.” Recruiting workers was her biggest problem.
Record subsidies to individuals during the pandemic is one reason people have not yet returned to the labor market, many manufacturing companies are saying.
“The situation is so severe, that despite the purchase of six acres of land, we put our expansion plans on hold. This is unsustainable,” Lantinen said.
Global supply chains today are too lengthy, too complex, too interdependent, too polluting and too subject to the risk of cascading delivery failure to be sustainable.
Companies that are doing well, like Toyota and Tesla, are those that have always made it a priority to keep suppliers close to the point of final production.
MADE IN AMERICA.
CPA is the leading national, bipartisan organization exclusively representing domestic producers and workers across many industries and sectors of the U.S. economy.
TRENDING
CPA: Liberty Steel Closures Highlight Urgent Need to Address Mexico’s Violations and Steel Import Surge
CPA Applauds Chairman Jason Smith’s Reappointment to Lead House Ways and Means Committee
Senator Blackburn and Ossoff’s De Minimis Bill is Seriously Flawed
JQI Dips Due to Declining Wages in Several Sectors as November Jobs Total Bounces Back from Low October Level
What Are Trump’s Plans For Solar in the Inflation Reduction Act?
The latest CPA news and updates, delivered every Friday.
WATCH: WE ARE CPA
Get the latest in CPA news, industry analysis, opinion, and updates from Team CPA.
CHECK OUT THE NEWSROOM ➔